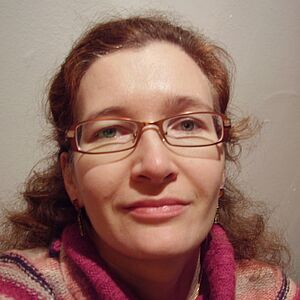
Nathalie Limodin
Axes de recherche
Les projets de recherche auxquels je participe:
Des modèles fiables de propagation sont essentiels dans les secteurs, i.e. énergie, transport, où la fissuration est une question de sécurité. Bien que les matériaux de structure soient sollicités en fatigue sous amplitude variable, l’effet de surcharges sur la fatigue reste ardu à prévoir. Le but du projet ADVENTURE est d’étudier cet effet sur des fissures de fatigue 3D pour construire des modèles prédictifs. Un couplage d’essais de fatigue sous tomographie synchrotron avec la corrélation de volumes numérique (CVN) permettra de comprendre ces effets en mesurant la fermeture le long du front de fissure et son évolution après surcharge. Pour obtenir une résolution élevée de la CVN et une fissure se propageant avec une forme adaptée à la modélisation, un alliage Al-Si à grains fins et un mouchetis naturel de particules de Si sera fabriqué. Les données expérimentales obtenues alimenteront un nouveau modèle de fissuration via une approche Data-Driven qui s’affranchit de la loi de Paris.
Le but d’ADVENTURE est d’étudier l’influence de surcharges pour construire des modèles prédictifs permettant de gérer des fissures de fatigue 3D, même courtes, avec une complexité et un effet d’histoire similaires à ceux rencontrés dans les structures réelles.
Des modèles fiables sont essentiels dans tout secteur où la fissuration est une question de sécurité. La relation entre vitesse de propagation avant surcharge et Facteur d’Intensité des Contraintes (FIC) est mise en défaut. Même si le phénomène est connu, les mécanismes restent controversés et, le plus souvent, étudiés en surface. Une compréhension des effets 3D résultant de la variation de taille de zone plastique le long du front de fissure requiert d’autres techniques expérimentales.
Le couplage d’essais de fatigue sous tomographie synchrotron avec la corrélation de volumes numériques (CVN) à haute résolution spatiale permettra de mesurer les déformations et leur évolution après surcharge. Pour obtenir une résolution élevée de la CVN, un alliage Al-Si à grains fins ad-hoc avec un mouchetis naturel sera fabriqué. Des essais 2D permettront d'élargir la base de données expérimentale.
Les données (champs de déplacement, fissures) 2D et 3D, inédites à cette échelle, alimenteront un nouveau Modèle de fissuration Incrémental, au même titre que la plasticité, et Généralisé (MIG), qui s’affranchit de la loi de Paris.
La vitesse de propagation étant liée à la plasticité en pointe de fissure, celle-ci sera mesurée par une approche Data-Driven et caractérisée par des descripteurs topologiques de la zone plastique formant un Indicateur d’Ecoulement Plastique (IEP). La fissure sera aussi décrite par un Facteur d'Intensité des Contraintes étendu (FIC++) incluant les contraintes T et B liées aux effets de structure/bridage. Le modèle MIG consiste à interroger la base de données expérimentale pour obtenir, lors d'une simulation numérique élastique, l'estimation de la vitesse de propagation à partir de l'évaluation du FIC++ le long du front de fissure et l'évolution de l’IEP.
La méthodologie proposée se résume ainsi :
- Un matériau de structure : un alliage de moulage Al-Si à grains fins avec particules de silicium ;
- Des essais de fatigue avec surcharge réalisés sous tomographie synchrotron pour distinguer les fines particules de Si et suivre la croissance 3D de fissures. Des essais 2D complémentaires permettant de varier les effets de structure/bridage ;
- Des mesures de champs 2D/3D permettant de comprendre les mécanismes agissant lors d’une surcharge par le suivi de la fissure et des vitesses de propagation mais aussi l’extraction de FIC++ ;
- Les données alimenteront la base du modèle MIG avec les FIC++ et les IEP déduits des champs de déplacement par une approche Data-Driven;
- La validation consistera à reproduire, par une simulation numérique 3D X-FEM utilisant le MIG, les observations expérimentales.
Ce projet collaboratif répond aux objectifs de l’axe “Matériaux métalliques et inorganiques et procédés associés”. Il permettra de comprendre les mécanismes de fissuration 3D en couplant des essais in situ avec des mesures d’une résolution inédite en 3D. La richesse des données expérimentales permettra de proposer et valider un nouveau modèle 3D de prédiction de la fissuration pouvant être implémenté dans n’importe quel logiciel. Des outils plus prédictifs donneront des structures plus fiables, par exemple dans le transport et l’énergie.
Partenariat
Les 4 partenaires de ce projet partageront leur expertise en métallurgie des alliages d'aluminium (CTIF), en essais de fatigue couplés à des mesures de champs (LaMcube) et réalisés in situ sous tomographie X (MATEIS) et en techniques d’identification Data-Driven (GeM).
Financement
Ce projet a été financé par l'ANR Générique 2020 – PRC - Projets de recherche collaborative au titre notamment de la priorité "Intelligence artificielle". L'aide ANR est de 540 617€ sur 4 ans. Le projet est labellisé par le pôle I-Trans consacré aux transports terrestres durables et à la logistique.
La société MG-VALDUNES et les établissements Université de Lille, Université Polytechnique Hauts-de-France, CNRS, et Centrale Lille se sont associé pour créer le laboratoire de recherche commun nommé SWIT’LAB (https://switlab.cnrs.com/) pour «Science for Wheelset Innovative Technology».
Le périmètre scientifique de ce projet est constitué des laboratoires LaMcube UMR 9013 (Université de Lille – Centrale Lille – CNRS) et LAMIH UMR CNRS 8201 (Université Polytechnique Hauts-de-France – CNRS).
Au sein de ce laboratoire, les partenaires s’engagent à travailler ensemble au service du développement d’une recherche de très haut niveau alliée à une stratégie d’implantation d’activités R&D et d’essais ferroviaires en Hauts-de-France.
L’ambition est de réunir des compétences complémentaires permettant d’améliorer les performances des organes de roulement ferroviaires, de créer des innovations procédés-produits et de réduire les coûts de possession produits en s’appuyant sur des expertises de recherche des laboratoires.
- Budget : 658 k€
- Coordinateur : P. Dufrénoy (LaMcube)
- Partenaires : MG Valdunes, LAMIH, LaMcube
L’étude de la fatigue nécessite souvent des matériaux ou des éprouvettes modèles avec, par exemple, une microstructure représentative d’un procédé industriel à l‘échelle d’une éprouvette qui permette de reproduire le phénomène à étudier dans des conditions maîtrisées.
L’objectif premier de la réalisation d’éprouvettes d'alliage d'aluminium à microstructure contrôlée est la maîtrise de la porosité qui a une influence cruciale sur l'amorçage des fissures de fatigue. La porosité dépend de la teneur en hydrogène mais aussi de la composition chimique de l’alliage (Fe, Sr, Mn, Si) et des conditions de solidification. La maîtrise de ces paramètres impose de maîtriser en interne toutes les étapes de l’élaboration.
Dans le cadre de l'ANR INDiANA et en collaboration avec le CTIF, nous avons, dans un premier temps, utilisé les outils de prototypage rapide à notre disposition à l’Ecole Centrale de Lille et les moyens de la plateforme MetaLIQ pour fabriquer des éprouvettes à microstructure maîtrisée en partant de la conception du moule jusqu’à la coulée selon la procédure schématisée ci-dessous.
La difficulté majeure réside dans le contrôle de la solidification afin d’obtenir, d’une part, une taille de microstructure caractéristique du procédé industriel et, d’autre part, une localisation des pores au centre de la zone utile d’une éprouvette de tomographie de section millimétrique. Ce type de microstructure ne peut être obtenu qu’en imposant un profil thermique bien déterminé lors de la solidification de l’éprouvette.
SPeCiMEn (https://lamcube.univ-lille.fr/equipements/) repose sur un four de fusion par induction en partie haute (acquis) et un moule avec un inducteur en partie basse (en cours de conception) centré sur le milieu de la longueur utile de l’éprouvette. Le moule comprend des refroidisseurs aux extrémités pour refroidir l’éprouvette par les têtes et imposer le profil thermique souhaité.
La Fabrication Additive Métallique est un secteur en forte croissance. Les technologies d'aujourd'hui demandent une expertise et des investissements très importants (~1M EUR), ce qui freine leur adoption. La diffusion de ces nouvelles méthodes requiert de nouveaux procédés plus abordables. De nouvelles technologies récentes, basées sur la technologie MIM (Metal Injection Molding), permettent l'avènement de machines moins chères (120k€). Ainsi, nous souhaitons consacrer un pôle d'excellence scientifique et industrielle à cette nouvelle technologie.
Notre objectif est de développer un procédé dont l'investissement global serait inférieur à 30k€ pour rendre ce procédé accessible aux TPE/PME et aux FabLabs. Pour passer du prototypage rapide à la fabrication additive, il faut être en mesure de prévoir les défauts dans les pièces, de maîtriser le procédé afin de prévoir les performances mécaniques des pièces produites. Nous répondrons à cette problématique par la conception de ce procédé « low-cost », le développement et la validation des outils de simulation dédiés.
- Budget total : 3568 k€
- Coordinateur : J-F. Witz (LaMcube)
- Partenaires : Machine 3D, Sirris, CRITT-MDTS, Université de Mons, Cenaero, Materalia, LaMcube