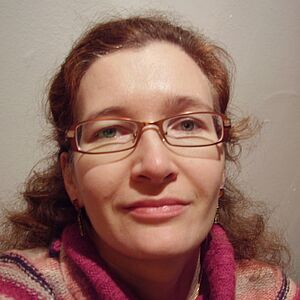
Nathalie Limodin
Research axis
Reliable Fatigue Crack Growth (FCG) models are crucial in all industries where fatigue cracks are a major safety concern such as in energy and transportation. While structural components are submitted to variable amplitude fatigue, the effect of overloads (OL) in fatigue life remains challenging to predict. The aim of the FATALE project is to understand OL effects on physically small 3D fatigue cracks to build predictive models. A coupling of in-situ fatigue tests under synchrotron tomography with Digital Volume Correlation (DVC) will allow understanding transient FCG by measuring crack closure along the crack front and its evolution with OL. In order to reach a high spatial resolution DVC and have a propagating crack with a shape suitable for modelling, a fine grained Al-Si alloy with a natural speckle of Si particles will be designed. The wealth of obtained experimental data will be used as an input for Data-Driven identification of a new 3D crack model not based on Paris law.
The aim of ADVENTURE is to study the influence of overloads on 3D fatigue cracks in order to build predictive models to manage even short cracks with a complexity and history effect similar to those encountered in real structures.
Reliable models are essential in all areas where cracking is a safety issue. Although structural materials are subjected to variable amplitude fatigue loading, the effect of overloads remains difficult to predict. After an overload, the relationship between the crack growth rate before overload and Stress Intensity Factor (SIF) fails. Although the phenomenon is known, the underlying mechanisms remain controversial and often studied on the surface. Understanding the 3D effects resulting from the variation in plastic zone size along the crack front requires further experimental techniques.
A coupling of fatigue tests under synchrotron tomography with digital volume correlation (DVC) will allow to measure the closure along the crack front and its evolution after overload. To obtain high resolution of the DVC, a fine-grained Al-Si alloy with a natural speckle will be fabricated. Tests will also be carried out in 2D on specimens allowing different structure/constraint effects to be obtained in order to extend the experimental database.
Indeed, the 2D and 3D data (displacement fields, cracks), never seen at this scale, will feed a new Generalized, compared to those in the literature, and Incremental, such as plasticity, Model (GIM), via a Data-Driven approach that breaks away from the Paris law.
Since the crack growth rate is related to plasticity, the plasticity at the crack tip will be measured by topological descriptors of the plastic zone forming a Plastic Flow Indicator (PFI). The crack will also be described by an extended Stress Intensity Factor (SIF++) including T and B stresses related to structural/constraint effects. The GIM model consists in using an interpolation/regression technique within the experimentally fed database to obtain, in a linear elastic numerical simulation, the propagation velocity estimate from the evaluation of the SIF++ along the crack front and the evolution of the PFI.
The proposed methodology can be summarized as follows:
- A structural material, a fine-grained Al-Si casting alloy with a speckle of silicon particles, will be developed to promote the propagation of a crack that is relatively easy to model;
- Overload fatigue tests will be carried out under synchrotron tomography to monitor 3D crack growth and distinguish fine Si particles. Tests will also be carried out with 2D observation on specimens allowing to vary the structure/constraints effects;
- 2D/3D field measurements from the tests will allow to understand the mechanisms at play during overload by monitoring the evolution of the crack and growth rates but also to extract the SIF++ and to interpret the mechanisms observed in the light of this parameter;
- These data will feed the database of the GIM model with the SIF++ and the PFI deduced from the displacement fields by a non-parametric approach;
- The validation will consist in reproducing the experimental observations by a 3D X-FEM numerical simulation using the GIM.
This collaborative project meets the objectives of the "Metallic and Inorganic Materials and Associated Processes" axis. It will enable the understanding of 3D crack propagation mechanisms by coupling in situ tests with measurements of unique resolution in 3D. The richness of the experimental data will allow to propose and validate a new 3D crack growth model that can be implemented in any software. More predictive tools will give more reliable structures, for example in transport and energy.
Partnership
The 4 partners of this project will share their expertise in aluminium alloy metallurgy (CTIF), in fatigue tests coupled with field measurements (LaMcube) and carried out in situ under X-ray tomography (MATEIS) and in Data-Driven Identification techniques (GeM).
Funding
This project was funded by the ANR Generic 2020 - PRC - Collaborative Research Projects under the priority "Artificial Intelligence". The ANR grant is 540 617€ over 4 years. The project is labeled by the I-Trans cluster dedicated to sustainable land transport and logistics.
MG-VALDUNES and the institutions Université de Lille, Université Polytechnique Hauts-de-France, CNRS, and Centrale Lille have joined forces to create the joint research laboratory named SWIT'LAB (https://switlab.cnrs.com/) for «Science for Wheelset Innovative Technology».
The scientific perimeter of this project consists of the LaMcube UMR 9013 (University of Lille - Centrale Lille - CNRS) and LAMIH UMR CNRS 8201 (Polytechnic University Hauts-de-France - CNRS) laboratories.
Within this laboratory, the partners are engaged to work together to develop a very high level research combined with a strategy of setting up R&D activities and railway tests in Hauts-de-France region.
The ambition is to bring together complementary skills to improve the performance of railway rolling stock, to create process-product innovations and to reduce product ownership costs by relying on the laboratories' research expertise.
- Budget : 658 k€
- Coordinator : P. Dufrénoy (LaMcube)
- Partners : MG Valdunes, LAMIH, LaMcube
The study of fatigue often requires model materials or specimens with, for example, a microstructure representative of an industrial process at the specimen scale that allows to reproduce the phenomenon to be studied under controlled conditions.
The primary objective in the production of aluminum alloy specimens with controlled microstructure is the control of porosity, which has a crucial influence on the initiation of fatigue cracks. Porosity depends on the hydrogen content but also on the chemical composition of the alloy (Fe, Sr, Mn, Si) and the solidification conditions. The control of these parameters imposes to control in-house all the stages of the manufacturing process.
Within the framework of the INDiANA ANR project and in collaboration with CTIF, we first used the rapid prototyping tools at our disposal at the Ecole Centrale de Lille and the facilities of the MetaLIQ platform to manufacture specimens with a controlled microstructure from mold design to casting according to the procedure outlined below.
The major difficulty lies in the control of solidification in order to obtain, on the one hand, a microstructure size characteristic of the industrial process and, on the other hand, a location of pores in the center of the gauge length of a tomography specimen with a millimetre section. This type of microstructure can only be obtained by imposing a well-defined thermal profile during the solidification of the specimen.
SPeCiMEn (https://lamcube.univ-lille.fr/equipements/) is based on an induction melting furnace in the upper part (acquired) and a mold with an inductor in the lower part (under design) centered on the middle of the gauge length of the specimen. The mold includes chillers at the ends to cool the specimen through the heads and impose the requested thermal profile.
Metal Additive Manufacturing is a fast growing sector. Today's technologies require expertise and very high investments (~1M EUR), which hinders their adoption. The diffusion of these new methods requires new and more affordable processes. Recent new technologies, based on MIM (Metal Injection Molding) technology, allow the advent of less expensive machines (120k€). Thus, we wish to dedicate a pole of scientific and industrial excellence to this new technology.
Our objective is to develop a process whose overall investment would be less than 30k€ to make this process accessible to SMEs and FabLabs. To go from rapid prototyping to additive manufacturing, it is necessary to be able to predict the defects in the parts, to control the process in order to predict the mechanical performance of the parts produced. We will address this issue by designing this "low-cost" process and developing and validating dedicated simulation tools.
- Total budget: 3568 k€
- Coordinator: J-F. Witz (LaMcube)
- Partners: Machine 3D, Sirris, CRITT-MDTS, University of Mons, Cenaero, Materalia, LaMcube